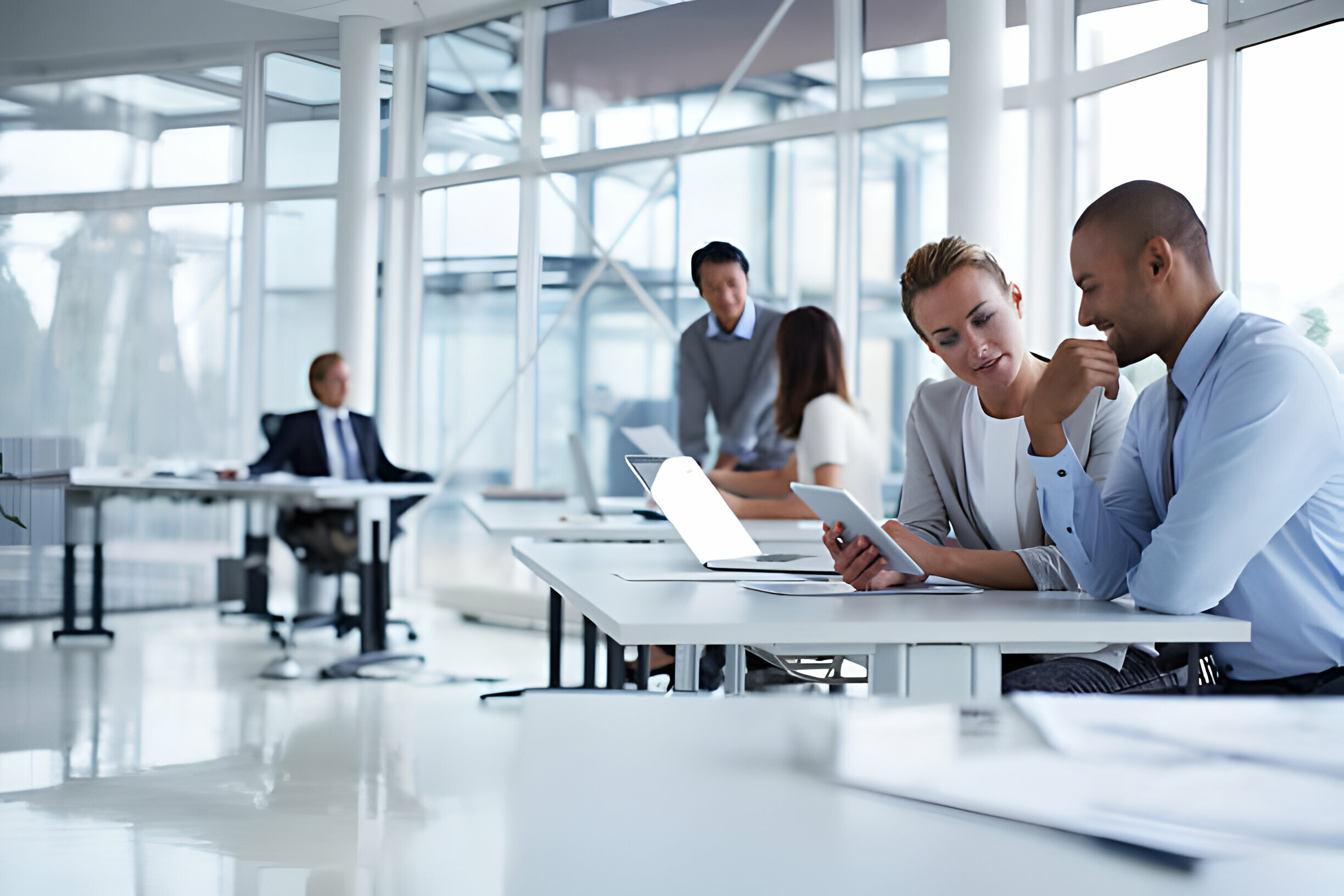
Lean Meaning
- Posted by zadmin
- Categories Lean Six Sigma Courses
- Date April 15, 2024
Unlocking Business Success: The Definitive Guide to Lean Process Improvement Principles and Benefits
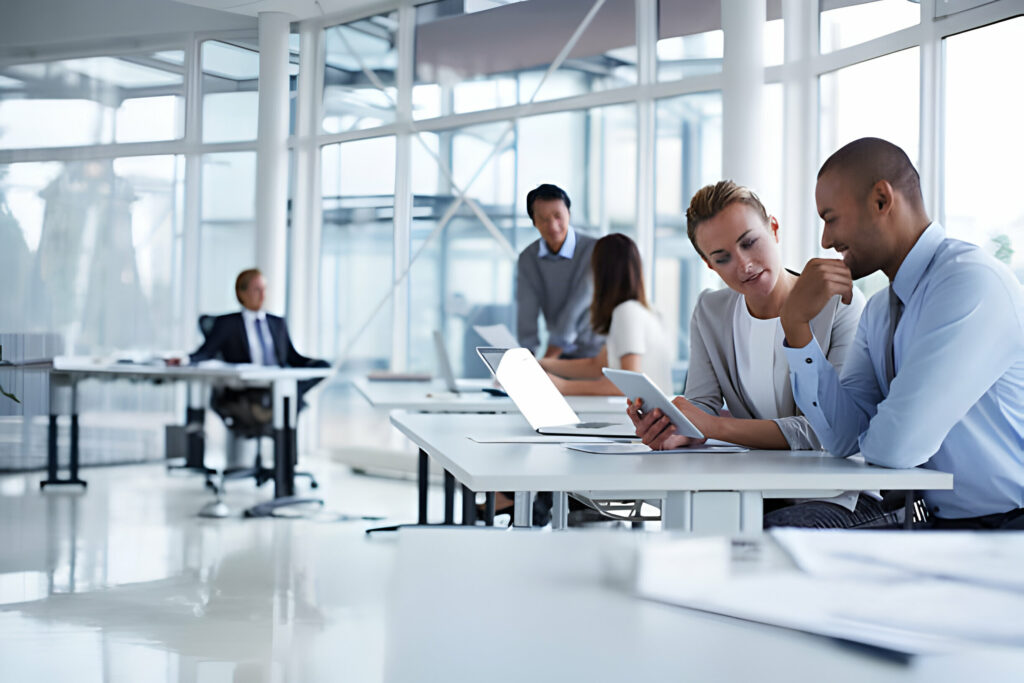
About Lean
Lean Process Improvement emerges as not just a methodology but a transformative journey towards sustainable success. By embracing Lean principles, organizations can navigate the evolving business landscape with innovation, collaboration, and excellence, ensuring their continued growth and prosperity in the 21st century.
Introduction to Lean meaning and Lean Process Improvement: Principles and Benefits
In today’s rapidly evolving and fiercely competitive business environment, enterprises perpetually pursue strategies to bolster operational efficiency, curtail waste, and augment overall productivity. Lean Process Improvement is a prominent methodology that has garnered substantial acclaim in addressing these imperatives.
Rooted in the manufacturing sector, Lean has organically evolved into a versatile framework with wide-ranging applicability spanning diverse industries, including but not limited to healthcare and IT services. Its principles initially honed on the shop floors, have seamlessly transitioned into a comprehensive approach for identifying and eliminating inefficiencies, ultimately ushering in a new era of streamlined processes and heightened performance across the corporate landscape.
In this in-depth article, we’ll explore the principles and benefits of Lean Process Improvement and meaning of lean, drawing insights from authoritative sources.
Understanding Lean Process Improvement
Lean Process Improvement, often called ” Lean, ” is a systematic strategy for locating and removing waste from processes, ultimately leading to improved quality, reduced costs, and enhanced customer satisfaction. It is rooted in delivering value to customers while minimising activities that do not contribute to that value. To better understand the principles of Lean, we can turn to the wisdom of experts in the field.
In “The Lean Six Sigma Pocket Toolbook” by Michael L. George, the author emphasises the core principles of Lean. George explains that Lean is built on five fundamental principles:
Identify Value: The first step in Lean Process Improvement is identifying what customers value in a product or service. This principle stresses the importance of aligning processes with customer needs and preferences.
Map the Value Stream: Once the value is identified, it’s essential to map the entire value stream, encompassing all the activities and steps required to deliver the product or service to the customer. This step helps identify areas of waste and inefficiency.
Create Flow: Lean encourages creating a smooth and continuous flow of work, minimising interruptions, bottlenecks, and delays. Achieving flow streamlines processes and improves lead times.
Establish Pull: Instead of pushing products or services onto customers, Lean promotes a pull system, where production is driven by customer demand. It reduces overproduction and excess inventory.
Seek Perfection: Lean is a continuous improvement process. Organisations should strive for perfection by identifying and eliminating waste, enhancing efficiency, and improving quality.
The Benefits of Lean Process Improvement
Now that we have a foundational understanding of Lean’s principles, let’s explore the tangible benefits it offers organisations.
The advantages of Lean Process Improvement:
Cost Reduction: One of the most immediate and noticeable benefits of Lean is cost reduction. Organisations can significantly reduce operational expenses by eliminating waste, leading to improved profitability.
Improved Quality: Lean principles emphasise delivering value to customers. As a result, quality is prioritised throughout the process, reducing defects and errors.
Enhanced Productivity: Lean promotes efficient and streamlined processes, leading to higher productivity. Employees are empowered to identify and eliminate bottlenecks, increasing output with the same or fewer resources.
Shorter Lead Times: Lead times are significantly reduced due to getting rid of waste and establishing flow. It allows organisations to respond to customer demands more rapidly.
Increased Customer Satisfaction: Lean focuses on delivering value and aligning processes with customer needs. Higher customer loyalty and satisfaction are the benefits of this.
Better Employee Engagement: Lean encourages employee involvement in process improvement. Employees engaged at work are more driven and dedicated, leading to better results.
Adaptability: Lean is not a one-size-fits-all approach. It can be adapted to various industries and processes, making it a versatile methodology.
Sustainability: Lean Process Improvement also has environmental benefits. Organisations minimise their environmental impact by reducing waste, making Lean a sustainable practice.
Real-world Application of Lean
To illustrate the practical application of Lean Process Improvement, let’s examine a real-world case study described in “Lean Thinking” by James P. Womack and Daniel T. Jones.
Case Study: Toyota’s Lean Journey
Toyota is often regarded as a pioneer in the implementation of Lean principles. The company’s journey towards Lean began in the 1950s when Taiichi Ohno, an engineer at Toyota, developed the Toyota Production System (TPS), later known as Lean Manufacturing.
At the heart of TPS and Lean is the concept of continuous improvement, or Kaizen. Toyota empowered its employees to identify and eliminate waste, focusing on processes rather than individual tasks. It resulted in significant improvements in quality, reduced lead times, and cost savings.
One of the most famous elements of TPS is the Andon system, which allows any employee to stop the production line if they identify a defect or problem. It prevented defective products from reaching customers and encouraged a culture of problem-solving and continuous improvement.
Toyota’s success with Lean principles led to the widespread adoption of Lean in manufacturing and other industries worldwide.
Conclusion
Lean Process Improvement is a robust methodology that offers numerous benefits to organisations across various sectors. Its core principles, including recognising value, outlining the value chain, establishing flow, establishing pull, and pursuing perfection, provide a framework for continuous improvement and waste reduction.
By embracing Lean, organisations can achieve cost savings, improve quality, enhance productivity, and, most importantly, deliver more excellent value to their customers. The real-world success stories of companies like Toyota are a testament to the transformative power of Lean Process Improvement.
As we navigate a quickly evolving business landscape, Lean remains a valuable tool for organisations intending to continue functioning and flourishing in the 21st century. It is not merely a set of practices but a mindset that encourages innovation, collaboration, and excellence. Lean Process Improvement is not just a methodology but a journey towards continuous improvement and sustainable success.
JK Michaels Institute offers certification in Lean and lean six sigma
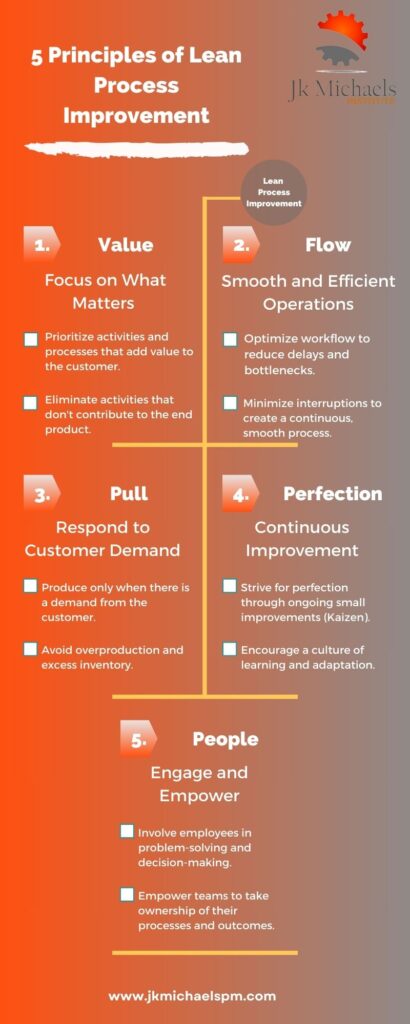
© 2025 All Rights Reserved.
Previous post
Mastering Agile Project Management Framework: Strategies for Success in a Dynamic World
You may also like
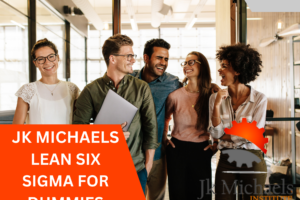
DMAIC SIX SIGMA
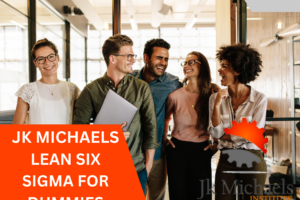
LEAN SIX SIGMA FOR DUMMIES
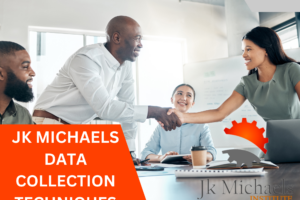