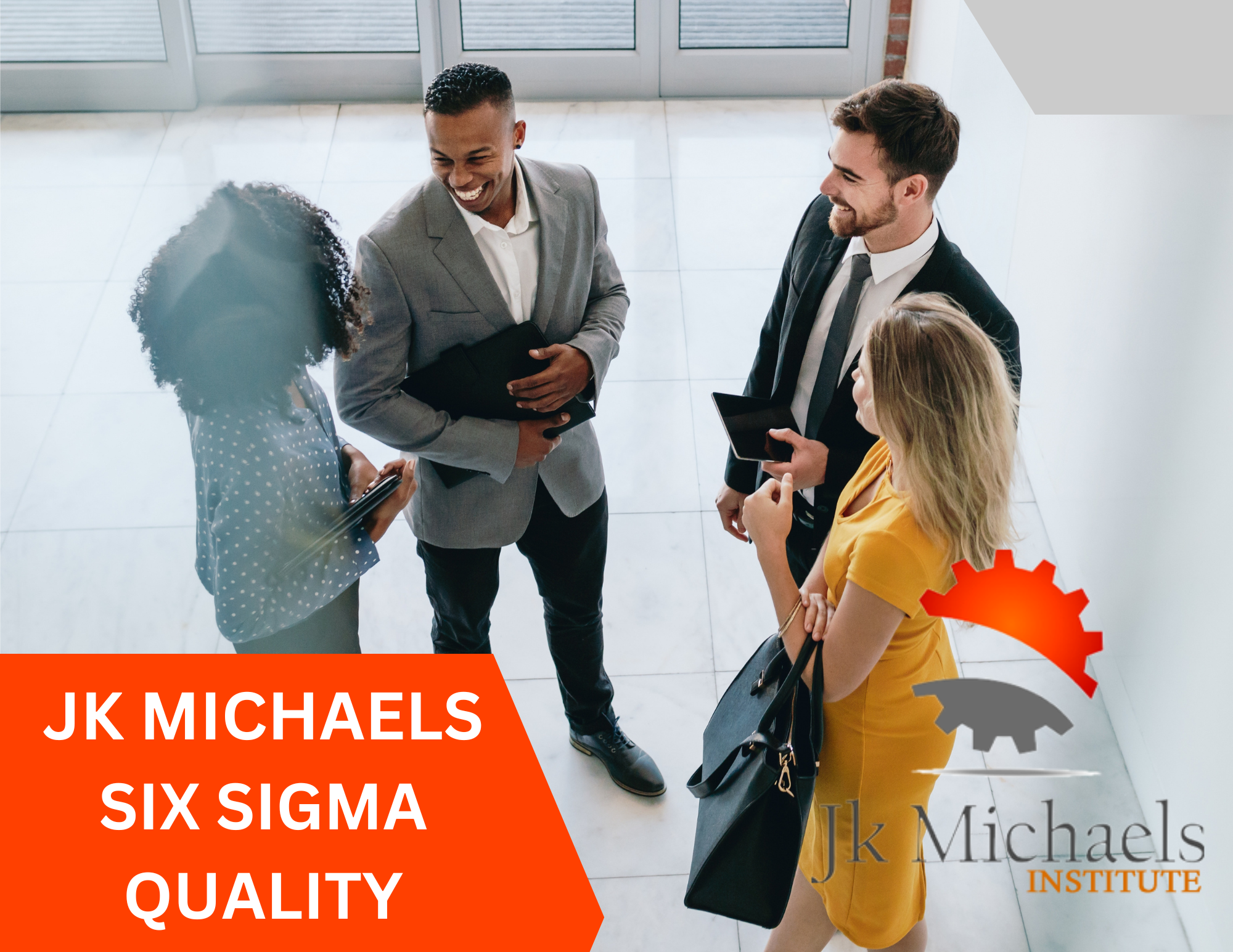
SIX SIGMA QUALITY
- Posted by zadmin
- Categories Lean Six Sigma Courses
- Date February 13, 2024
Six Sigma quality
Six Sigma quality usually refers to a well-controlled process (i.e., requirements/tolerance limits 6s from the center line and process limits 3s from the center line in a control chart).
Differing opinions on the definition of Six Sigma
What is Lean Six Sigma?
Six Sigma and Lean integration
Putting Six Sigma into Practice
Six Sigma tools
Certifications in Six Sigma
DISPUTING VIEWS ABOUT WHAT DEFINES SIX SIGMA
Although the following definitions of Six Sigma differ, they all have certain things in common:
The utilization of groups with clearly defined tasks directly affects the company’s bottom line.
Offering comprehensive training in advanced statistics and project management to essential personnel and training in “statistical thinking” at all levels. These crucial individuals are known as “Black Belts.” Examine the many roles, levels, and belts in Six Sigma.
It focuses on the DMAIC (define, measure, analyze, improve, and control) problem-solving methodology.
The management style sees these projects as a viable business plan.
Philosophies: From a Six Sigma conceptual standpoint, all work can be defined, monitored, analyzed, improved, and managed. Inputs (x) are needed for processes to produce outputs (y). Controlling the inputs will give you control over the outputs. Typically, this is written as y = f(x).
Set of tools: The Six Sigma specialist uses qualitative and quantitative methods or instruments to promote process improvement. These tools include process mapping, failure mode and effects analysis (FMEA), control charts, and statistical process control (SPC). Six Sigma experts are divided regarding the precise instruments that make up the package.
Methodology: The fundamental and exacting DMAIC technique is acknowledged in this Six Sigma perspective. The DMAIC outlines the procedures that a Six Sigma practitioner must adhere to, beginning with problem identification and concluding with the application of durable solutions. Although other Six Sigma methodologies are in use, DMAIC is unquestionably the most popular and well-known.
Metrics: A 1.5-sigma shift in the mean corresponds to 3.4 faults per million opportunities or Six Sigma quality performance.
Six Sigma Quality Performance
LEAN SIX SIGMA: WHAT IS IT?
While lean focuses on eliminating waste (non-value added processes and procedures) and promoting work standardization and flow, Six Sigma focuses on minimizing process variation and improving control. Six Sigma and lean are no longer easily distinguished; in fact, the phrase “lean Six Sigma” is becoming more and more common since process improvement needs elements of both methodologies to produce desirable outcomes.
Lean Six Sigma is an improvement philosophy that prioritizes defect prevention above fault detection and is fact-based and data-driven. By lowering variance, waste, and cycle time and encouraging the usage of work standardization and flow, it generates a competitive advantage and improves customer satisfaction and bottom-line results. It should be implemented whenever there is variance and waste, and all employees should be involved.
Six Sigma on ASQTV™
Exclusive to ASQ members: Seven webcast series on lean Six Sigma tools:
Overview: Kaizen Flow, Value Stream Mapping, 5S Seven Wastes, Visual Workplace, Customer Voice (Open access)
Boeing Merging SIX SIGMA AND LEAN
Customers should expect the highest levels of quality, cost, delivery, and, as of late, nimbleness from both Lean and Six Sigma. Although there is a lot of overlap between the two disciplines, they take slightly distinct approaches to their shared goal:
• Six Sigma places more emphasis on variance reduction than Lean does on waste reduction.
Lean uses less technical techniques like visual controls, workplace organization, and kaizen to accomplish its goals, while Six Sigma typically uses statistical data analysis, experiment design, and hypothesis testing.
Successful implementations frequently start with the lean methodology, which aims to maximize workplace effectiveness and efficiency while cutting waste and utilizing value stream mapping to enhance comprehension and throughput. More sophisticated Six Sigma statistical techniques may be used if process issues persist.
SETTING UP SIX SIGMA
Organizations may have different Six Sigma deployment methodologies depending on their unique cultures and strategic business objectives. An organization that decides to apply Six Sigma has two main choices:
Put in place a Six Sigma project or program.
Establish a Six Sigma infrastructure.
First option: Put in place a Six Sigma initiative or program.
This method involves periodically training specific employees (practitioners) in statistical tools and asking them to use them as needed. If the practitioners still require assistance, they may speak with a statistician. There may be successes; however, these do not reinforce one another to promote further and improved utilization of the tools and overall system.
When a company implements Six Sigma as a program or initiative, it frequently has just added a few new, unorganized items to its toolbox through training sessions. Applying the tools as necessary to assigned projects is one way to expand on this strategy. Nevertheless, it’s crucial to remember that choosing, overseeing, and carrying out initiatives are not usually essential functions of the company.
There may be particular difficulties when putting a Six Sigma program or initiative into action. These initiatives, which are frequently developed at a low level inside the company, could not have the support of senior management, which could result in opposition from other groups that the initiative would affect. Furthermore, no one is usually tasked with championing initiatives across organizational boundaries and facilitating change.
Typically, a Six Sigma program or initiative does not provide the infrastructure necessary for projects linked to the organization’s strategic goals to produce bottom-line advantages. As a result, it needed more support to generate a significant return on the training expenditure.
Executive-level backing and management buy-in are essential for real success. It may facilitate the adoption of other Six Sigma techniques and statistical tools across organizational boundaries.
Establishing a Six Sigma Infrastructure is Option 2.
It is optimal when Six Sigma training offers a process-oriented approach that teaches practitioners a methodology to choose the right tool for a predefined project at the right time rather than concentrating on the individual tools. Using this method, Six Sigma training for practitioners (Black Belts) usually consists of four weeks of instruction spread across four months, with students spending the three weeks in between sessions working on their projects.
It is more efficient to use projects rather than tools when implementing Six Sigma as a business strategy to maximize the time and financial investment in Six Sigma training.
Take into consideration the following advantages of implementing Six Sigma through projects supported by executive management:
Provides more significant effect through initiatives linked to financial performance,
makes more targeted and effective use of the tools and gives a studyable and adaptable project management approach or strategy.
Project presentations improve communication between managers and practitioners,
make it easier to comprehend essential business procedures in detail,
and explain to management and staff how statistical tools may be precious to businesses.
Provides input on project methodology to Black Belts throughout training; applies Six Sigma in a closed-loop manner, allowing for audits and integrating lessons gained into a broader business plan.
A good project selection process is essential to a project-based approach. Projects that align with the objectives of a company’s business plan should be chosen. Then, Six Sigma can be applied as a roadmap to achieve those objectives successfully.
In the beginning, businesses may have projects that are too big or that aren’t selected because of how they will strategically affect their bottom line. An important lesson learned from the first round of projects is that frustration can spur development in the second.
Six Sigma requires a sustained commitment. Objectively Analyzing the deployment process enables examining all its components, including project selection and scoping. If the company takes the time and devotes the executive energy required to execute Six Sigma as a business strategy, using lessons gained and incorporating them into the following waves of an implementation plan provides a closed feedback loop and spectacular bottom-line benefits!
You may also like
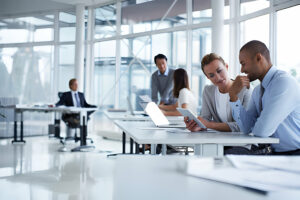
Lean Meaning
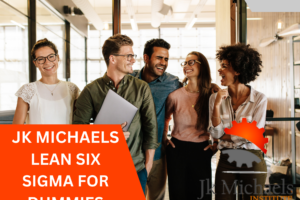
DMAIC SIX SIGMA
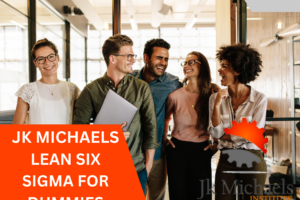