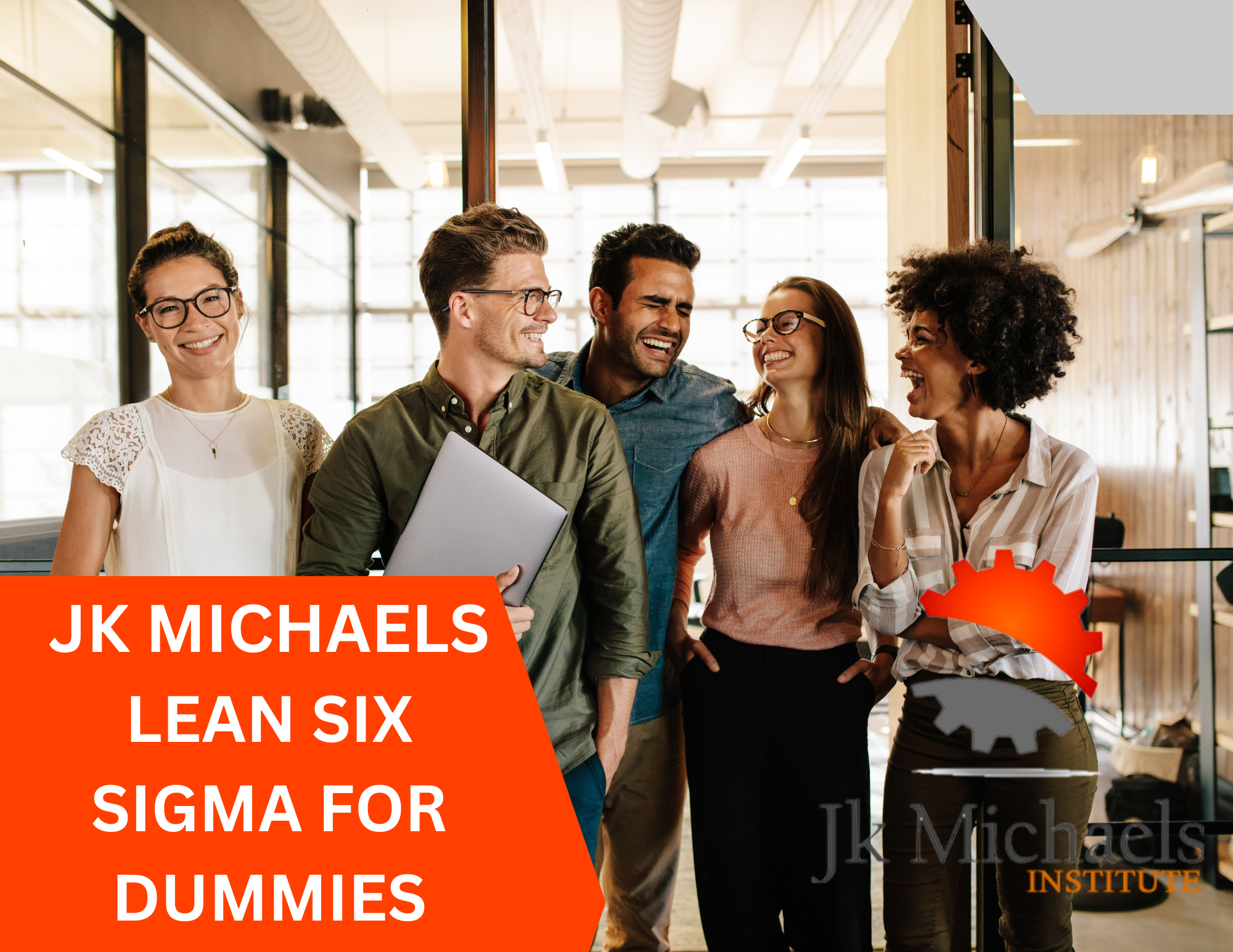
LEAN SIX SIGMA FOR DUMMIES
- Posted by zadmin
- Categories Lean Six Sigma Courses
- Date February 13, 2024
Lean Six Sigma for Dummies: Are you considering Lean? Not in terms of losing weight, but in terms of productivity? Lean Six Sigma for Dummies is another resource that might help you adopt a lean mentality. Lean Six Sigma is a well-liked process optimization technique applied in many businesses. It is an excellent example of removing waste and streamlining operations. You can maximize your team’s productivity, projects, and organization by implementing the ideas described in this book.
Lean Six Sigma for Dummies, written by two professionals with over 20 years of experience in teaching Lean Six Sigma, breaks down this organizational practice’s jargon, highlights the fundamentals of both Lean thinking and the Six Sigma method, and provides simple instructions.
Create a continuous improvement culture by implementing Lean Six Sigma.
Automate robotic processes to finish monotonous jobs.
Evaluate how well your staff and business have adapted to Lean Six Sigma.
Learn how to apply Lean Six Sigma daily.
Look for best practices to maintain continuous advancements.
Lean Six Sigma For Dummies demonstrates how to apply Lean Six Sigma in every industry and at any size organization with practical checklists and insightful guidance. To properly adopt the Lean Six Sigma mindset, pick up a copy.
Are you prepared to implement the tried-and-true Lean Six Sigma techniques to boost team productivity and enhance corporate performance? To ensure that your business operates efficiently and effectively, remind yourself of the fundamentals of this effective method.
The fundamental ideas of Lean Six Sigma
Lean Six Sigma is a potent, tried-and-true technique for raising business productivity and effectiveness. In summary, the following are the main Lean Six Sigma concepts to remember:
Pay attention to the client.
Determine and comprehend the work process (the value stream).
Control, enhance, and ease the flow of the process.
Eliminate waste and non-value-adding steps.
Reduce variation and manage based on facts.
Engage and prepare the participants in the process.
Engage in systematic improvement activities.
How Lean Six Sigma Uses DMAIC
To apply Lean Six Sigma to your current business processes in an organized manner, you must make use of the helpful DMAIC framework:
Define: Every project begins with an issue that has to be resolved. Ensure that everyone working on the project knows the responsibilities, the purpose of the endeavor, and its goals.
Measure: Your effort throughout the defined stage was predicated on your perception of the issue. Please clarify during the Measure stage by seeing how well the work is completed.
Examine: Having established the nature of the issue, it’s time to determine its cause but avoid drawing hasty judgments. In actuality, be able to investigate potential causes and identify the underlying problem.
Enhance: Alright, you are aware of the procedure and the issue. To address the core reason, you must generate several ideas in the Improve step, choose the best one, and test it.
Control: You must put the answer into practice and make sure you obtain and maintain the desired gain. Establishing a control plan is essential to ensuring the procedure is followed correctly.
Lean Six Sigma Value
Keep in mind that value is determined by what your consumers are willing to pay for when applying Lean Six Sigma to improve value for them:
The appropriate goods and services
In the ideal moment and at the ideal cost in the appropriate quality
A step needs to fulfill three requirements to be considered value-adding:
The step must be critical to the customer.
The step must either be a necessary precondition for another step or physically alter the good or service.
It is necessary to complete the step “right the first time.”
Try to eliminate any stages that don’t fit these requirements, but be aware that you might need to keep specific non-value-adding steps around for other reasons, such as legal or budgetary constraints.
The value stream must be recognized and understood, and waste and steps that do not create value must be removed. As little as 10 to 15 percent of the process steps, or about 1 percent of the entire process time, can add value.
How to use Lean Six Sigma to combat waste
Lean Six Sigma can optimize process flow in several ways, one of which is waste reduction. The acronym Tim Wood can occasionally be used to identify the following seven categories of waste:
Transportation: the needless movement of goods and materials.
Inventory: An excess of work-in-progress or stock arising from overproduction.
Motion: inadequate placement of groups or apparatus.
Waiting: Delays can result from, say, equipment failure.
Overprocessing: Executing pointless stages of processing.
Overproduction: when goods are produced more than required or too soon after.
Imperfections: Handling redo work.
You may also like
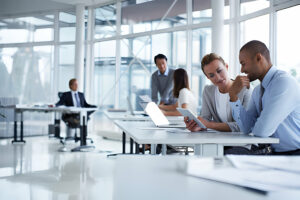
Lean Meaning
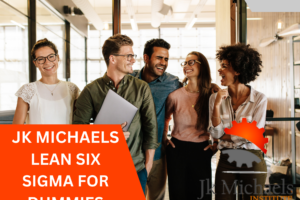
DMAIC SIX SIGMA
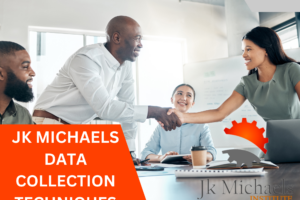