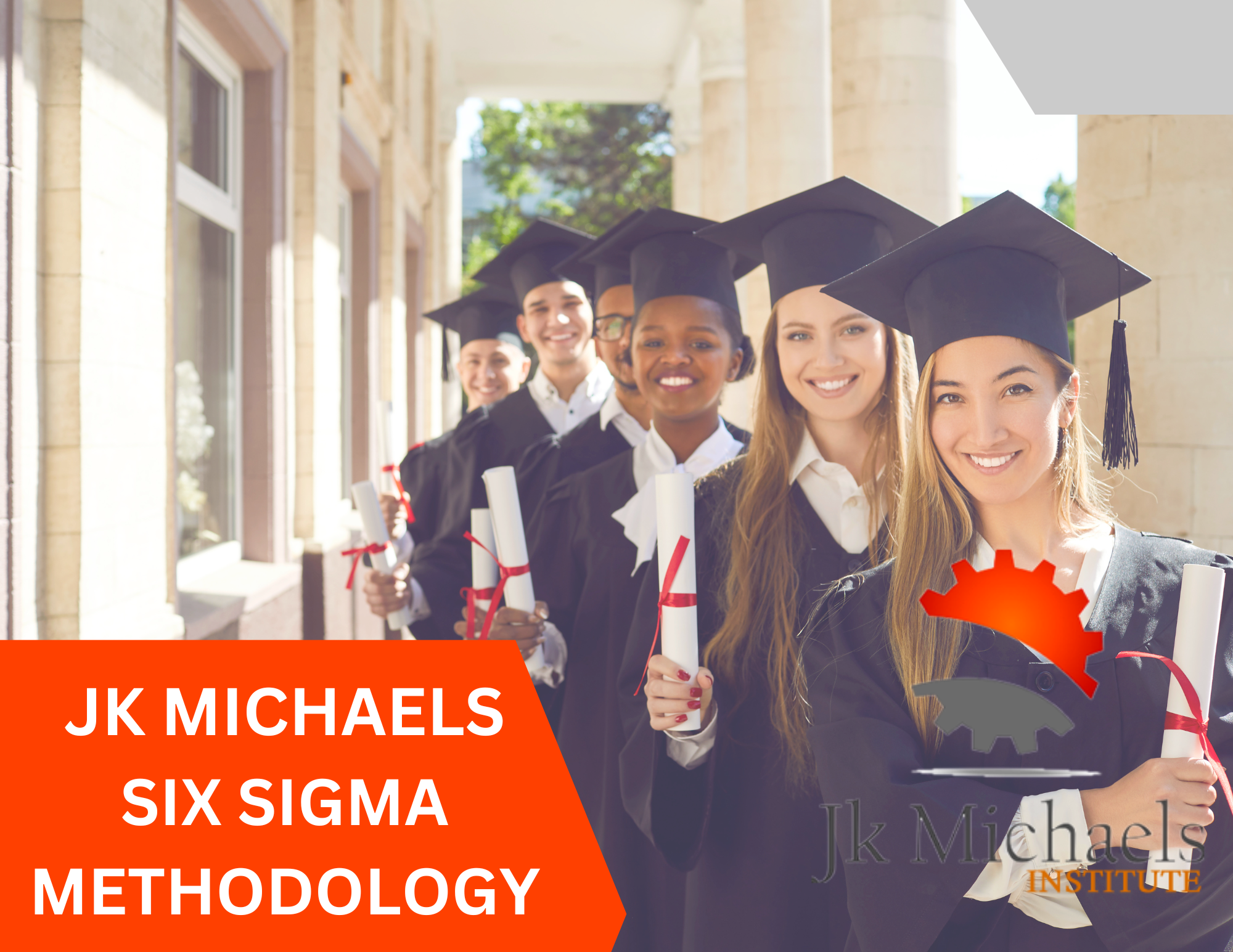
SIX SIGMA METHODOLOGY
- Posted by zadmin
- Categories Uncategorized
- Date February 9, 2024
Six Sigma methodology is a strategy for process improvement that uses data and statistical analysis to reduce defects, waste, and errors, and increase customer satisfaction and profits. It was created by Motorola in 1986 and popularized by General Electric in 1990s. It aims to achieve a six sigma level of quality, which means 3.4 defects for every one million opportunities. It can be applied to any business process, from manufacturing to management. It provides tools and techniques to define, measure, analyze, improve, and control each step of a process.
Methodologies of Six Sigma.
Within Six Sigma, two primary approaches are divided into five portions each.
DMAIC: Improving current business processes is the primary use of the DMAIC technique. The symbols represent:
Define the issue and the objectives of the project.
Measure every facet of the current process in great detail.
Analyze data to, among other things, identify the core flaws in a process.
Improve the process.
Control how the process is done in the future.
DMADV: New procedures, goods, or services are usually developed using the DMADV method. The symbols represent:
Define the project goals.
Measure the capabilities of the product and essential process components.
Analyze the data, create a few different process designs, and select the best one.
Design and test the details of the process.
Run pilot programmes and simulations to confirm the design, then turn the process over to the client.
Six Sigma also makes extensive use of management tools. The following are a few instances:
Five Whys
This approach finds the source of an issue by asking five questions at a time. The approach is straightforward: after stating the ultimate issue (the car wouldn’t start, I was late for work again today), ask “why,” which will lead to the solution and reveal the underlying cause of the problem. In these two situations, it may be because I need to leave my house earlier to get to work on time or because I neglected to maintain the automobile properly.
CTQ Tree
The elements of a process that yield the features required in your product and service if you want happy consumers are broken down in the Critical to Quality (CTQ) Tree diagram.
Root Cause Analysis
This approach, similar to the Five Whys, is how a company tries to find the source of a problem and fix it instead of just fixing its “symptoms.”
All Six Sigma techniques and technologies aim to optimise company processes to generate the most significant goods and services with the fewest errors. Firms worldwide are adopting it, demonstrating its extraordinary success in the current economic climate.
You may also like
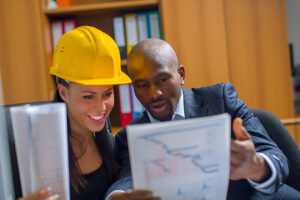
Cost Estimation Techniques in Project Management
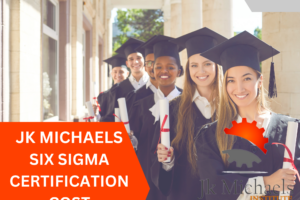
SIX SIGMA CERTIFICATION COST
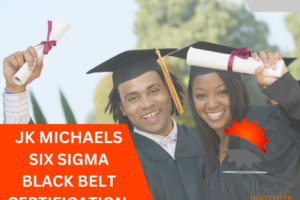