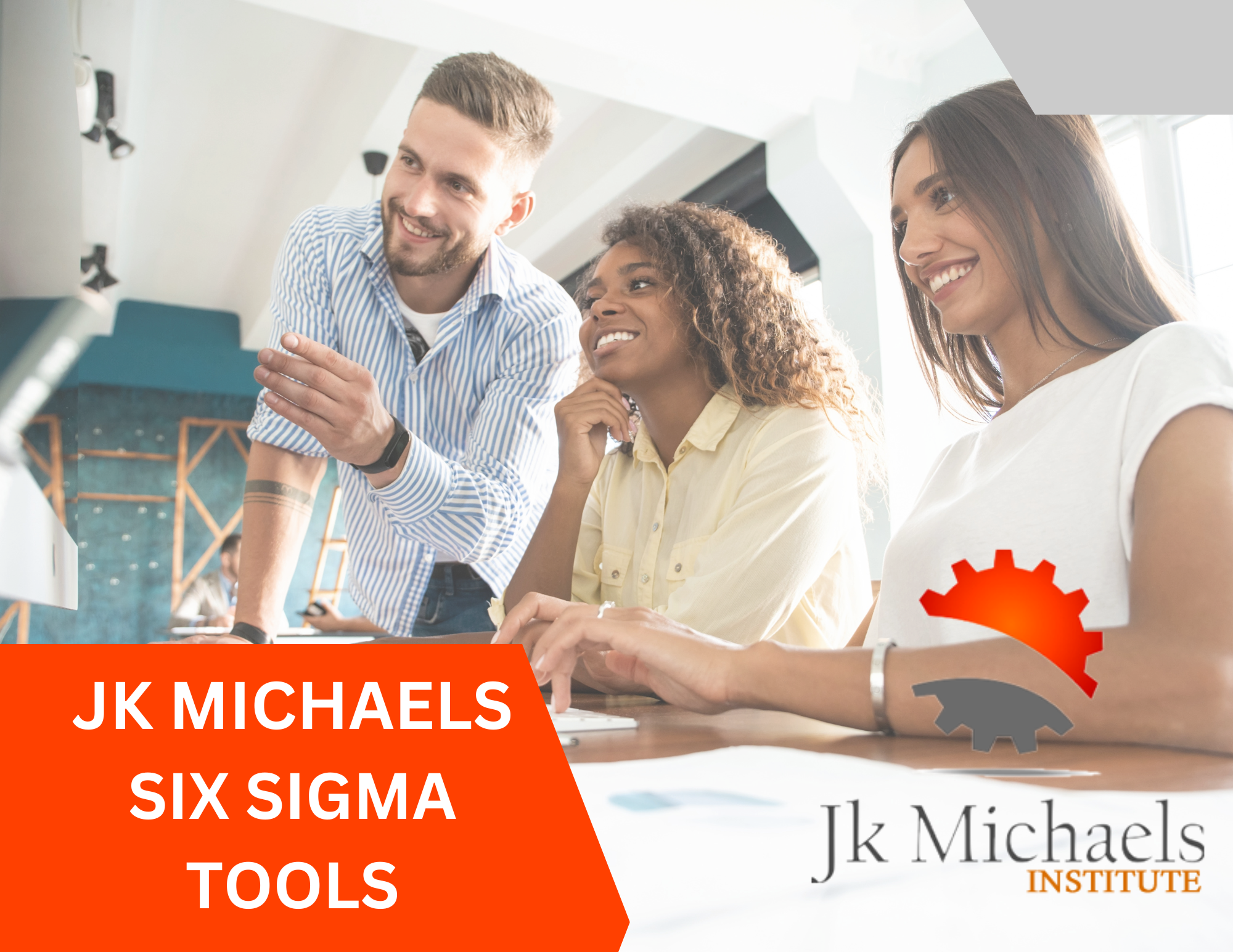
SIX SIGMA TOOLS
- Posted by zadmin
- Categories Lean Six Sigma Courses
- Date February 8, 2024
SIX SIGMA TOOLS
Six Sigma tools refer to the problem-solving instruments utilized with other process improvement initiatives. The Six Sigma specialist uses qualitative and quantitative methodologies to promote process improvement. While the instruments are not new, how they are used and incorporated into a system is. Several statistical and graphical instruments frequently employed in projects aimed at improvement include:
A data-driven quality strategy for process improvement is DMAIC (define, measure, analyze, improve, and control). It is a crucial component of Six Sigma projects, but it can also be used as a stand-alone quality control method or in conjunction with other processes, like lean.
5S:
To assist in cutting waste and maximize production, the Five S’s of lean methodology produce a clean, uncluttered, safe, and well-organized workplace. Its purpose is to foster a high-calibre work environment, both psychologically and physically. Any workspace suitable for lean manufacturing and visual control can benefit from the 5S philosophy.
Seven Wastes:
Seven inefficiencies Reducing and eliminating waste is a fundamental lean principle. The seven wastes include overproduction ahead of demand; waiting for the following process: worker, material, or equipment; needless material transportation; overprocessing parts due to inadequate tool and product design; keeping more inventory than is necessary; needless employee movement while working; and the production of defective parts.
Value stream mapping (VSM)
Value stream mapping is a two-stage process that can be carried out with a pencil and paper. Make a visual depiction of each step in the material and information flows by following a product’s production cycle from start to finish. Second, sketch out how value should flow in the ideal future state. The map showing the future status is the most crucial one.
Flow:
Without stoppages, scrap, or backflows, a product moves smoothly from design to launch, order to delivery, and raw to finished materials in the customer’s hands. Flow is the progressive accomplishment of tasks along the value stream.
Visual workplace:
A visual workplace makes human and machine performance safer, more accurate, predictable, and dependable; a visual workplace is characterized by gadgets transmitting information about organizational activities.
Voice of the customer:
The first step in the Quality Function Deployment (QFD) process is to identify and investigate the customer’s demands. It develops a voice of the customer table (VOCT); the voice of the customer (VOC) must first be captured. User support forums, helplines, social media, warranty claims, sales, and technical trip reports are familiar sources.
Project management techniques like Gantt charts and team engagement methods like the nominal group approach and brainstorming are also utilized by Six Sigma team leaders.
You may also like
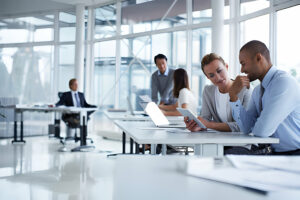
Lean Meaning
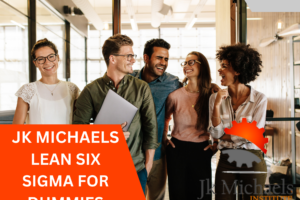
DMAIC SIX SIGMA
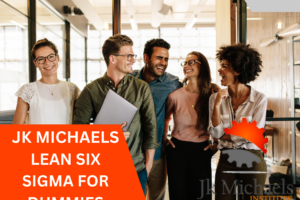